ディスペンサーの使いこなし術:塗布タイミングと粘度管理の極意
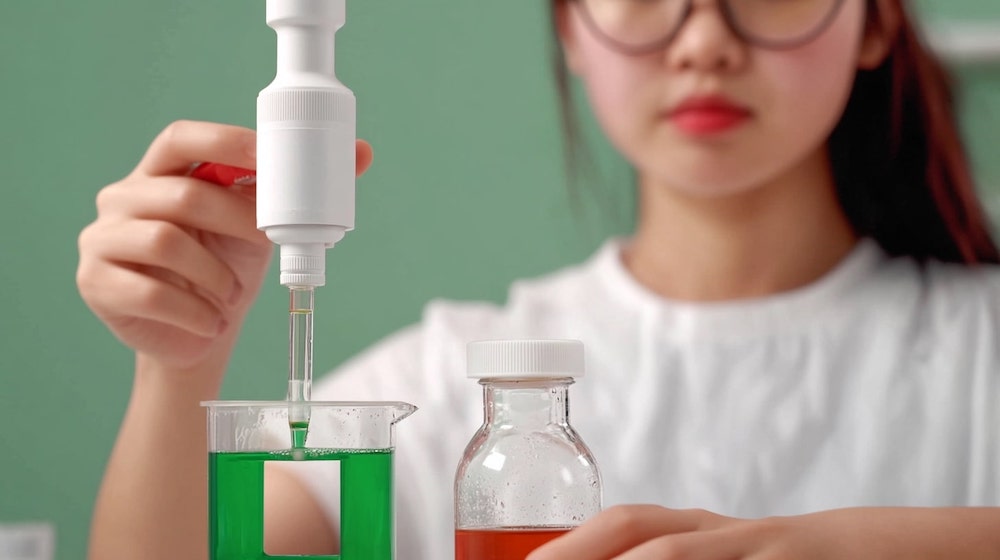
ディスペンサーは、製造工程における接着剤や塗布材を一定量・一定タイミングで供給するための装置です。
かつて私も、自動車部品メーカーや工作機械メーカーで自動化ラインの研究開発を進めるなか、ディスペンサーの塗布精度向上に幾度となく挑んできました。
「わずかなタイミングのズレが品質に大きな影響を与える」――そんな現場を見てきたからこそ、ディスペンサーの真価は、塗布タイミングと粘度管理を徹底的にコントロールする点にあると考えています。
本記事では、実際の製造現場で起こりがちな塗布ズレのメカニズムや、粘度管理をどう最適化するかについて、私の経験を交えながら解説します。
読み終えた頃には、「現場ならではの課題」を踏まえたうえでディスペンサーを使いこなし、より安定した生産性と品質を手に入れるためのヒントが得られるでしょう。
目次
塗布タイミングを攻略する
塗布ズレが起こるメカニズムと対策
ディスペンサーを使うとき、最も注意すべきなのが“塗布ズレ”です。
ロボットアームやコンベアとの位置合わせが不十分だったり、制御信号の遅延やノズルの目詰まりが起きたりすると、狙った箇所に正確に塗れません。
特に電子部品や自動車部品のように寸法精度が厳格な製品では、微小なズレが大きな不良につながります。
対策としては次のポイントを押さえましょう。
- サイクルタイムの把握:ディスペンサーと他の装置(ロボット、コンベアなど)の稼働周期をシミュレーションしておく。
- 制御信号の見直し:PLCやセンサーの設定を細かく調整し、実際の動きと同期するタイミングを入念に検証する。
- ノズル清掃・交換の計画:吐出不良は塗布ズレの原因となるため、定期的なメンテナンス計画を立てる。
自動化ラインでのタイミング同期:成功事例から学ぶ
私が以前手がけた自動化ラインでは、ロボットアームが複数の工程を素早くこなす一方で、ディスペンサーのノズル吐出に微小な遅延が生じる問題がありました。
そこで採用したのが「アームの軌跡とノズルのオン・オフタイミングを再計算し、必要に応じて補正信号を送る」という仕組みです。
結果として塗布ズレが大幅に減り、ラインの稼働率向上に貢献できました。
こうした成功のカギは、「ロボットアームとディスペンサーを別々に扱わず、一体のシステムとして制御する」ことにあります。
粘度管理の極意
適切な粘度が生む品質安定と作業効率
ディスペンサーで安定した塗布を実現するうえで、粘度管理は欠かせません。
粘度が低いと、塗布量が増えすぎてはみ出しや気泡混入のリスクが高まります。
逆に粘度が高すぎると、ノズル詰まりや断続的な吐出によって、塗布ラインが途切れる原因にもなります。
粘度を適切に保つことで、余分な材料を使わずに済み、歩留まり(不良率)の低減にもつながるでしょう。
また、粘度の安定はオペレーターの作業負荷を軽減し、生産現場全体の効率アップに寄与します。
粘度調整の実践手法:温度・素材・装置設定の見直し
粘度調整で多くの現場が見落としがちなのは、「温度」と「素材特性」の相互作用です。
たとえばエポキシ系接着剤は、室温が変化すると粘度が大きく変わることがあります。
そのため、製造ラインの環境温度を一定に保つか、装置内に温調機能を設けるなどの工夫が有効です。
さらに、粘度に合わせてディスペンサー側の圧力やノズル径を変更するのも重要なポイントです。
一見面倒に思えるかもしれませんが、装置設定をこまめに見直すだけで、目に見えて歩留まりが改善するケースが多々あります。
「粘度の最適化は塗布の安定化。塗布の安定化は品質の安定化。」
これは私が現場で常に意識している言葉です。
なお、チューブ入り液剤をそのまま使用できるエア圧送式 チューブ入り液剤用ディスペンサ(1液型ディスペンサー)のような製品も市販されています。
チューブを専用のタンクにセットする仕組みであり、微少量吐出が可能なため、温度や素材特性に左右されやすい液剤を扱う際にも重宝するでしょう。
チューブ交換が容易でメンテナンス効率も高いため、粘度管理の面でも一つの有効な選択肢となります。
ディスペンサーのメンテナンスと継続的改善
日常メンテナンスのポイントと頻度
ディスペンサーを長期的に安定稼働させるためには、日常的なメンテナンスが欠かせません。
- ノズルの清掃:最低でもシフトごと、もしくは材料交換のタイミングで行う。
- シール部品の点検:老朽化や摩耗があると微細な漏れが起き、粘度変化や吐出不良の原因になる。
- 制御系のログ確認:稼働データをこまめに解析し、異常値が出ていないか早期に把握する。
こうした基本的な点検を怠ると、塗布タイミングや粘度管理がいくら完璧でも、想定外のトラブルで生産性が低下する可能性があります。
データ活用による塗布精度の継続的アップデート
近年はセンサー技術の進歩により、ディスペンサーの吐出量やノズル先端の温度などをリアルタイムでモニタリングできるようになりました。
そのデータを活用し、粘度や吐出タイミングを都度最適化することで、塗布精度のさらなる向上を期待できます。
たとえば、AIを利用した予測保全システムと連携することで、故障の前兆を把握し、計画的なメンテナンスへつなげる事例も増えています。
まとめ
ディスペンサーの塗布タイミングと粘度管理を正しく押さえることで、材料ロスの減少や不良率の低下、作業効率の向上といった大きなメリットを得ることができます。
私自身、研究開発や現場導入の経験を通じて感じてきたのは、「ディスペンサーはただの機械ではなく、ものづくり現場の可能性を広げる鍵」だということです。
新しい技術を導入する際には、まず塗布ズレや粘度変化がもたらすリスクをしっかり把握し、適切な制御や調整を施すことが肝心です。
そうすることで、現場の技術者一人ひとりが自信を持ってディスペンサーを扱い、品質向上と生産性アップを両立できるようになるでしょう。
今後もディスペンサーは自動化ラインの重要な要素であり続け、私たちの「ものづくり精神」をさらに高みへと引き上げてくれるはずです。